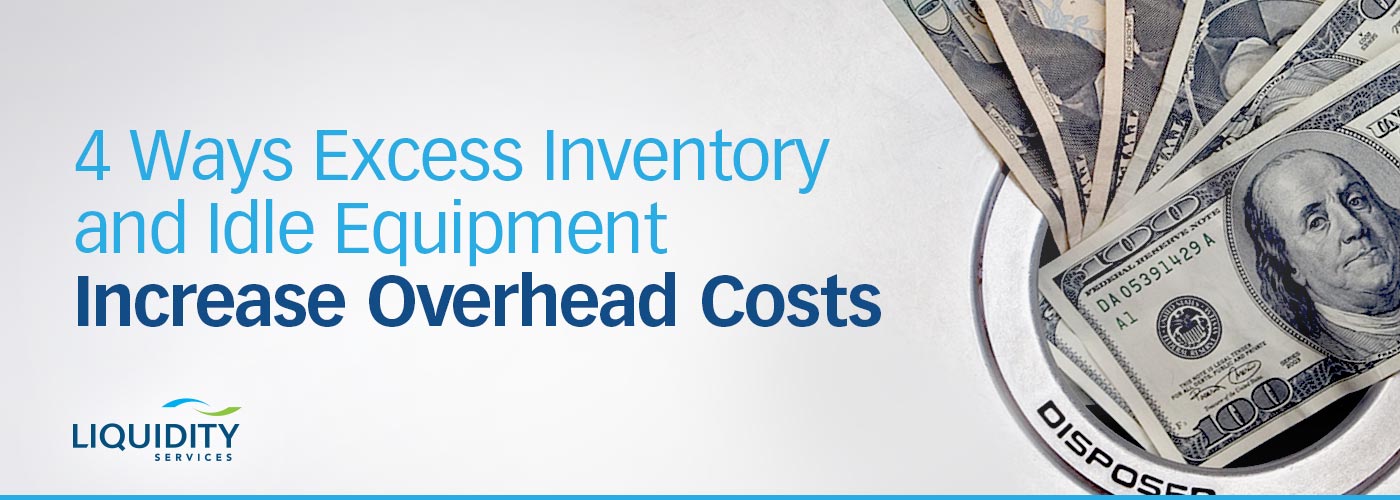
Maybe you’re waiting out the U.S. trade war with China, or you’ve got an eye on the hard Brexit date. Or, maybe you’re just in the middle of some expected seasonal downtime. Whatever the reason, you have mothballed equipment not being used, stockpiled supplies, and excess inventory that’s overflowing your warehouses. Every day you’re storing idle equipment and inventory, though, is a day you’re wasting thousands in overhead costs that could’ve been better spent elsewhere.
$32,000+ of Wasted Space in Your Warehouses and Factory Floors
Don’t believe it? Let’s do some quick math.
A recent warehouse industry survey puts the average cost of warehouse space at $6.53 per square foot. And, 64% of U.S. warehouses are at least 25,000 square feet, according to the United States Energy Information Association.
So, if fifteen to twenty percent of your warehouse or factory floor is effectively an “extra equipment” museum, then you’re throwing away $32,000+ every year. And, that’s just a ballpark estimate! If you have entire warehouses dedicated to excess inventory or returned stock that sits for months at a time, that’s a real money sink on your hands.
9+% Maintenance Costs for Excess Inventory and Equipment
All equipment needs repairs – all inventory stay pristine – if it will ultimately be useful for the company. This includes labor costs to maintain equipment and warehouse space. Sometimes, this also includes environmental maintenance costs for sensitive materials, like temperature and humidity maintenance.
Maintenance budgets normally reserve about 5-6% of the machine or inventory’s market value for labor expenses with an additional 3-4% for needed supplies. Plus, there’s an extra 1-2% for building maintenance expenses.
In all, you can expect to spend anywhere from 9 to 12% of your idle equipment or inventory’s market value on maintenance alone – and it’s not making your company a dime.
Beyond Capital Asset Depreciation: Your Increased Real Estate and Employee Tax Burden
On top of the space and maintenance costs for idle equipment and extra inventory, there’s an increased tax burden to consider.
Sure, capital assets like equipment and materials may be tax-advantaged through depreciation. But, you still pay real estate taxes for your commercial properties, and taxes on your employees’ compensation.
Every day you’re storing equipment that’s not producing goods or excess inventory that’s not available for purchase, you spend thousands in taxes for the privilege of hoarding it.
Higher Insurance Service Costs for Equipment, Products, Supplies and Excess Inventory You’re Not Using
Overhead for businesses includes necessary insurance payments ranging from professional liability to workers’ compensation. Property insurance pays for repair or replacement of equipment, inventory, supplies – anything inside the insured commercial building – should something happen.
Let’s estimate that commercial property insurance costs between $1,000 and $3,000 for every million dollars of coverage. In addition to covering your active lines and current products before they’re shipped to customers or stores, your commercial property insurance also covers idle equipment, unneeded supplies, and returned inventory.
Between insurance, taxes, maintenance, and storage – that’s tens of thousands you’re spending to keep unused and unwanted property. What else could you have spent that money on? Employee retention through training and benefits? Upgrading equipment? Product development?
And imagine how much more you could invest if you go an extra step further and sellthose formerly worthless assets to other businesses. That idle equipment and extra inventory becomes a new revenue opportunity instead of an unavoidable sunk cost.
Comments are closed.