Closing a facility is a difficult task, as it usually involves redeploying, selling, or disposing of millions of dollars of real estate, manufacturing equipment, systems and other surplus assets. All of this is in addition to personnel management, logistics, budgeting, inventory and maintaining the timeline for the closure.
As an additional challenge, facility closures must also adhere to an ever-evolving set of government regulations and industry standards. Failure to achieve compliance with these requirements can lead to onerous legal penalties and damage to your brand. With so much public focus on environmental safety these days, many organizations have internal sustainability metrics they must meet as well.
With all of this in mind, a facility closure and ensuing dismantlement can be thought of as a major construction project in reverse, with the added complexity of undoing years of operations and changes. That is why every phase of the closing process must be carefully planned and monitored to avoid safety, environmental, legal and financial problems.
Closing a site is a complex challenge, but the process can be simplified by following the four key steps of the Project Lifecycle: Initiation, Planning, Execution, and Close Out. This article will explain these four steps in detail.
1. Initiation
During the initiation phase, you define the preliminary analysis of the project objectives and ensure that further project work is authorized. This phase includes:
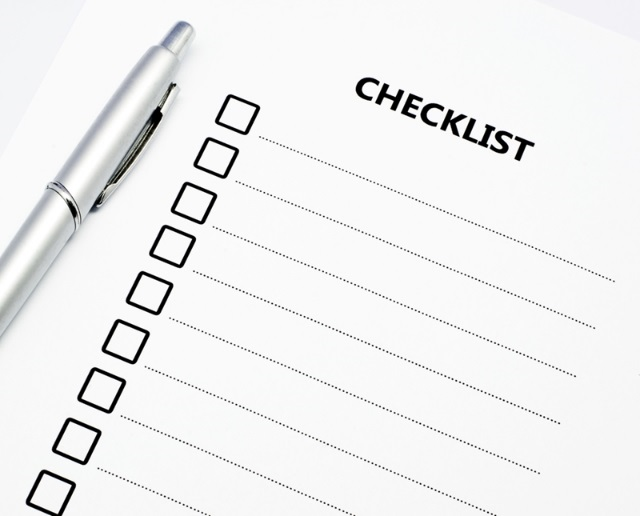
- Defining the scope of the project
- Setting goals and objectives
- Documenting project costs and benefits
- Developing a project charter
- Obtaining project authorization
Before the shutdown starts, every stakeholder involved with the project should closely coordinate with each other to build a clear blueprint for moving the plant from production mode to shutdown, cleanup, Investment Recovery and dismantlement. To get this started, the project manager must clearly define – in writing – the scope of the work, the timeline, and any local issues such as safety and environmental concerns, unemployment, etc., that might affect the project.
2. Planning
A closure plan will help you determine the budget and timeline for the management, valuation, redeployment, sale and removal of assets. Every plan should include the following three elements:
- Statement of work. This is a formal document that captures and defines the work activities, deliverables and project timeline. It usually also includes detailed requirements and pricing, with standard regulatory and governance terms and conditions
- Project cost elements and benefits. This is a documented project cost and benefit analysis.
- Confirmed corporate goals, timeline and executive sponsor. This ensures that project management and the rest of the business are aligned.
Additionally, your plan must identify the project team. The team in charge of the facility closure should include personnel from each functional area of your business and should be very familiar with your facility to ensure a streamlined, compliant closure.
Managing surplus assets is a major component of every facility closure, but many organizations lack the internal resources to handle this on top of everything else they need to do. This is where an external surplus asset management partner comes in. A partner can help you achieve sustainability goals, mitigate compliance risks, offer redeployment solutions and maximize your recovery on sales of your surplus assets. You should identify a partner early on in the planning phase to ensure that it is working in conjunction with the rest of your team and meets your timeline.
The last step in the planning process is to inventory all assets in your facility and determine which should be redeployed and which should be sold on the secondary market. This should begin three to six months prior to the plant closing its doors. An outside partner can efficiently inventory your assets, saving you time and money. Be sure to choose a partner with extensive industry experience to help you determine the best course of action for each of your surplus assets.
3. Execution
This phase involves the solicitation and award of agreements, project management team activation, the start of the project, and monitoring, controlling, and reporting on performance.
Managing quality assurance is critical throughout the execution stage of the closure. The project management team should conduct regular walkthroughs and reviews, hold daily safety inspections and audits, monitor costs and timeline variances and develop regular status reports.
Keeping open lines of communication is critical here. All concerned parties, such as the owner, contractors and consultants, should meet regularly to review progress and identify potential problems
Finally, any assets that cannot be redeployed should be sold on secondary markets. Your partner can help you achieve maximum recovery by giving you accurate asset valuations, determining the best sales channels for your surplus, leveraging targeted marketing strategies, scheduling a preview period for potential buyers and other key steps for successful sales for surplus.
During the Close Out step, you should look at your performance metrics to determine if your facility closure was a success.
4. Close Out
The remaining work of the project team involves releasing resources to other projects, developing lessons learned for future improvement, and closing out the administrative elements of the project from an organizational perspective. A checklist of the final activities to be completed should be maintained and checked off as each is done:
- Completing any close permits.
- Managing project acceptance.
- Conducting a close-out meeting.
- Ensuring that all deliverables have been completed and all measurable success indicators have been met.
- Documenting and sharing project results and lessons learned.
- Reviewing and recognizing team performance.
- Reviewing and recognizing financial performance.
- Closing the project records, updating and archiving project documentation, and making sure that all close-out conditions have been met.
Businesses often face the prospect of closing facilities as they consolidate business units or expand into new markets. Following this blueprint for a successful closure, in addition to working with a trusted surplus asset management partner, can make these processes easier and less expensive, ensuring you maximize the value of your assets to fuel the achievement of your future strategic goals.
Liquidity Services has experience maximizing value for site closures in a variety of industries. You can contact us today to learn more about our surplus asset management solutions.
Comments are closed.